Injection moulding is the process of injecting molten plastic into a mould under high pressure to create a repeatable part of good dimensional stability. Sounds simple right?
Well sometimes it is, depending on your quality requirements and part design. However, most of the time, unless it is a cheap toy with no aesthetic or structural performance requirements it can be a pretty tricky process involving many variables.
One very difficult application of injection moulding is thin walled injection moulding due to fact that you are trying to force a highly viscous fluid into a very small space under high pressure. Most injection moulding will have a nominal wall thickness of 2-4mm if the application allows, but you can inject as low as 0.3mm thickness with the correct equipment, plastic material and experience. One major road block and something that you might not be able to overcome is a very thin part with a long flow path. The longer the path to 100% fill the cavity the harder it is to push the plastic into all the nooks and crannies of the part.
Anyway, the point of this blog is to talk about proper mould (Tooling) venting design to try and make it possible to mould your thin walled part. Without good venting design it could be impossible to fill the part, or you might manage to fill the part but end up with lots defects and one being residual stress in the part causing performance or visual defects.
So, what is venting? Venting is as it sounds, a vent in the tooling cavity to allow air to escape when injecting the molten plastic because the mould tooling is made (should be made) to such a high tolerance that it can create an air tight seal in the cavity. So, imagine trying to push a syringe full of fluid that is blocked at the other end. Pretty tough right?
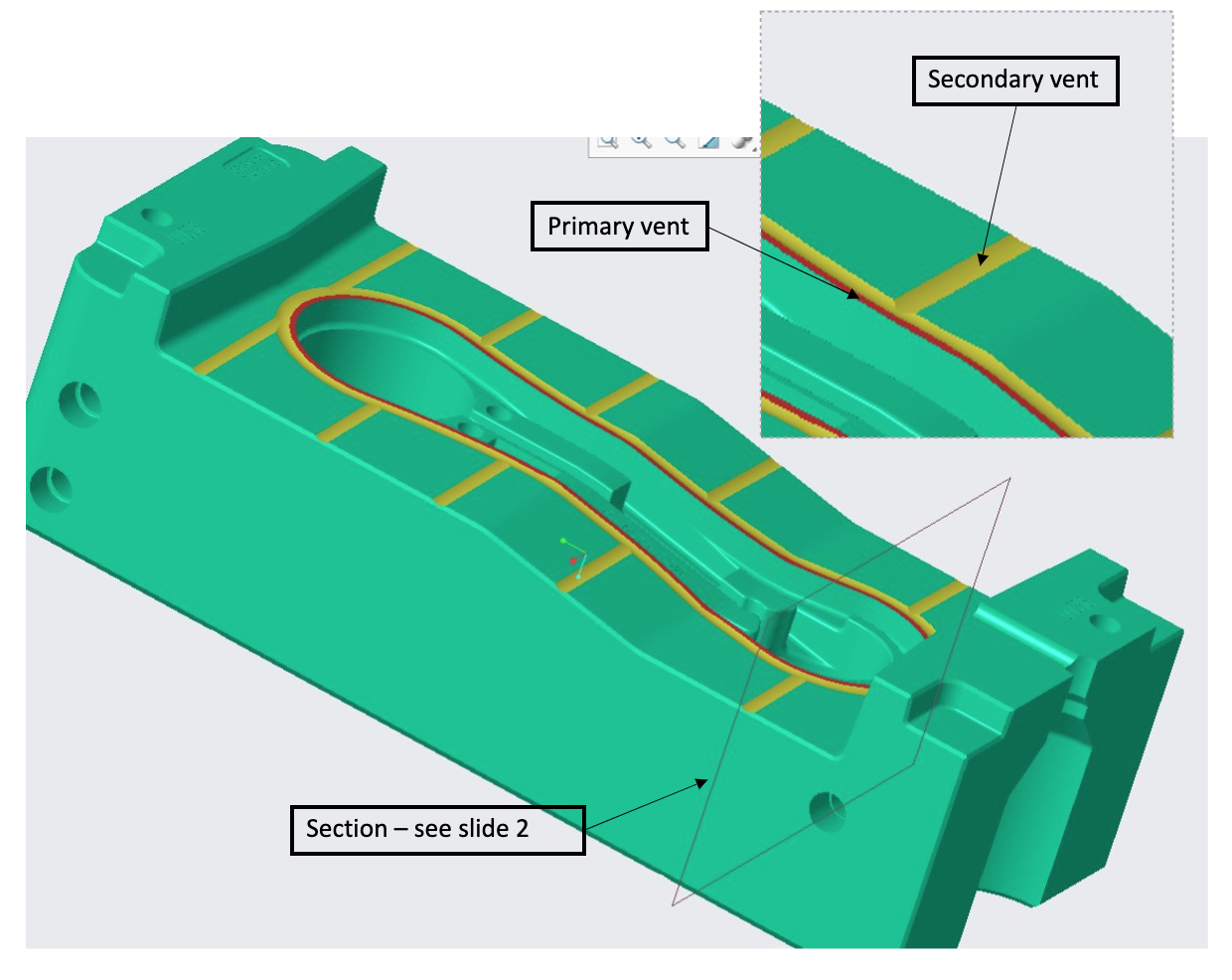
When injecting plastic into a long and thin part you need to have a high speed or rate of injection. Possibly up to 1000mm/s if you have the correct machinery. If you don’t have the correct venting design then you won’t be able to push the plastic at a high speed without creating a lot of opposing pressure on the the plastic flow front which will slow it down causing it to cool before 100% fill leaving residual stress in the part, warpage, a reduction of mechanical performance or a short shot and many more defects.
Thus, venting is a very important part of the process of mould tooling design. Ideally when designing the mould you would look at the material processing guide by the plastic material supplier as there will be different advice given for different materials.